Footwear construction can get a bit complicated to the untrained eye. That’s why we’re breaking down the anatomy of footwear to provide a better understanding of how it’s made. This will also help you make an informed decision about footwear that best fits your needs. So let’s get started…
Lasts
The word last comes from the old Anglo-Saxon word “lasest,” which means footprint.
The last is where the shoe is born and achieves its character. It largely determines the fit and feel of the shoe and also bears great influence on the shoe’s wear performance (tread, balance, shape holding ability, etc.) It’s also responsible for the shoe’s shape, which is a prime fashion factor in its look.
From inception through 1960, lasts were made from wood. Since then, lasts have been made from plastic because it doesn’t shrink or swell like wood. This produces truer sizes and a more consistent fit.
Last technology uses a multitude of measurements in order to balance fit and make consistent adjustments when customizing the last.
Uppers
The leather is the preferred shoe upper material. The following qualities make it one of the top components for shoe manufacturing:
- Breathability: Pores in leather allow fresh air to circulate inside the shoes.
- Moisture absorbency: Leather absorbs moisture away from the foot and out of the shoe.
- Customization: Leather will assume the shape of the wearer’s feet, providing individualized fit. This quality maximizes comfort and minimizes foot disorders.
- Durability: Leather resists tearing and puncturing.
Natural Uppers
- Side Leather: Side leather is the most versatile leather used. It gets the name because the hides are normally split down the back into two sides. Patterns can be imprinted, creating embossed leather. It can also be tumbled and crushed to become soft and drapeable. When side leather is impregnated with oils, it is sometimes called wax hide or waxy leather.
- Calfskin: This leather is from the young cows or calves. It has a fine grain and is soft and pliable. It also has the ability to withstand hard wear and combines elegant luxury with practicality.
- Kidskin: The skin of goats that is lightweight, yet strong and resilient.
- Exotic Leathers: Alligator, lizard, snake skin, or ostrich are common exotic leathers tanned from the hides and skins of these reptiles and birds.
- Pigskin: The skin of pigs or hogs is normally used as sueded or brushed leather. It’s also used for shoe linings.
- Nubuck: This leather finish is created by buffing the outer surface of the leather to produce a very fine nap.
- Patent Leather: This finish is produced by coating the surface of the leather with a film or urethane resin to give a high gloss.
- Suede Leather: Made by buffing the flesh or underside of the skin (kid, calf, pig or side leather) is how this finish is created.
Man-made Uppers
Man-made materials and fabrics are also used to make shoe uppers. The primary families of man-made imitation leathers are vinyl and urethane. Nyteck, Cordura, nylon/nylon mesh, and ballistic nylon are other examples.
Among the benefits of using man-made materials are generally lower materials cost, good looks, and easy maintenance. However, they have two primary disadvantages:
- Man-made materials do not absorb and pass off foot moisture.
- They lack memory retention and return to their original shape after being worn.
Height
The height of a boot is determined by measuring from the top of the sole, or the welt, to the top of the collar. In other words, the height of the boot does not include the height of the sole.
Lacing Systems
Below, hooks and eyelets are shown as part of lacing systems. You may also see D-rings in some footwear. Each has their own value for use. All help maintain a sturdy hold to keep your boots or shoes firmly on your feet.
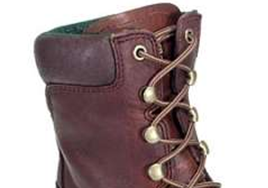
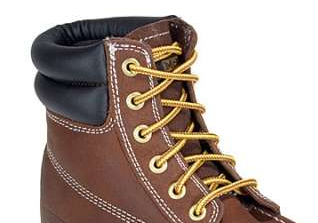
Linings
Linings are designed to improve footwear breathability. Customers might be inclined to think a boot is insulated when it has a lining, so make sure to understand the intended function of this feature. Footwear can be unlined or include Dri-Lex, Dryz, nylon mesh, Cambrelle, and Taibrelle linings, for example.
Insulation
Thinsulate™ branded insulation is the most common type used in footwear offered by Working Person’s Store. The amount of insulation is measured in grams. After reading the information on Thinsulate™ at www.workingperson.com, you will see that even the manufacturer believes that 400-600 grams is the best range of insulation.
Non-Removable Footbeds
(Examples: Poron, Padded/Pillow Cushion)
• The padding usually maintains cushioning for 6-8 months, depending on wear, exposure to water, and the amount of perspiration produced by the user.
• It isn’t uncommon for a boot wearer to create a hole in the padding under the big toe. Some people curl their toes without realizing it. Over time, the toe curling may result in a hole being worn in the padding.
Removable Footbeds
(Examples: EVA, Tri- or Dual-Density, Polyurethane)
Be very careful when choosing replacement insoles. Some people will have the logic that the more insoles they put in their shoes, the more comfortable the shoes will be. This is not necessarily the case. There are two problems with this thinking:
- Shoes are usually designed to accommodate ONE footbed. Placing two in the footbed can make them fit too tightly.
- Most footbeds are built up in the arch area which can interfere with the fit of the shoe. Placing two insoles would have a big effect on the arch support.
Choosing new work footwear and maintaining your existing boots and shoes is a lot easier once you know the ins and outs of their designs. This footwear construction guide was created to benefit workers like you, so visit Working Person’s Store the next time you need to update or upgrade your footwear!